Polyaspartic Concrete Coatings
Polyaspartic floors provide many years of heavy-duty use in virtually any environment including garages, hangars, firestations, warehouses, factories, restaurants, hospitals & health care facilities, kennels, showrooms, food processing, and more. They can be applied over most concrete surfaces including previously painted, tile, or even glued down carpet. Polyaspartic not only tops off the professional look, but also resists oil, beads water, and wipes clean like a kitchen counter top.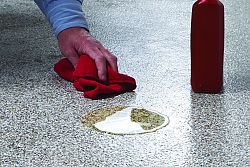
Our Polyaspartic flooring is available in color flake and solid colors. The color-flake floor offers a wide assortment of colors that burst to life and hide annoying imperfections in the concrete. Not only are the color-flake floors easy to maintain, but they have high stain, scratch, wear and UV resistance.
Benefits of Polyaspartics
- Rapid curing with a pot life that varies between 20 to 60 minutes (this is why the Polyaspartic installations can be completed in one day)
- High abrasion resistance (anywhere from 3-5x as abrasion resistant as Epoxy!)
- Can be applied at surface temperatures from 0º F to 120º F (Epoxy can’t be installed if the temperature is less than about 50º F)
- Very low viscosity (almost like water—that is why it forms such a strong bond to concrete)
- UV Stable (Epoxy will yellow in the sun. Rhino Polyaspartic will never yellow in the sun)
- Made with very high solids content (which allows Polyaspartic to be a “green” product—made without volatile organic compounds (VOCs) that pollute the air)
- Resistant to hot tire pick up and most all stains and chemicals (strong acid and methyl ethyl ketone (MEK) are the only known “kryptonite” for Polyaspartic. It is highly resistant to all other stains and chemicals)
Polyaspartic Vs. Epoxy
Description | Polyaspartic | Epoxy |
---|
Install time |
One day |
3-4 days |
Return to service |
Next day |
4-5 days |
Abraison resistance |
4x superior |
ASTM D 968 |
Unlimited build of film thickness in 1 coat* |
Yes |
No |
Odor |
Very Low |
HIGH |
VOCs |
VOC Free |
High VOCs |
High solid content |
Yes |
no |
Application temperatures |
as low as 32° F - 0° C |
above 55° F |
Elongation / expands with surface / joint |
Yes (50> Epoxy) |
No |
Color stability |
UV Stable |
Non-UV Stable |
Gloss retention |
Very Good |
Poor |
Chemical resistance |
Great |
Poor |
5 Step Application Process
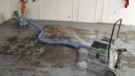 |
Step 1: Remove old surface and mechanically open up the floor by diamond grinding. |
 |
Step 2: Address cracks and pits. |
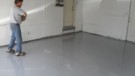 |
Step 3: Apply base coat and non skid additive
Step 4: Apply decorative color flakes. |
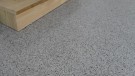 |
Step 5: Apply top coat(s) and let dry. |
Click each image below to see an enlarged view:
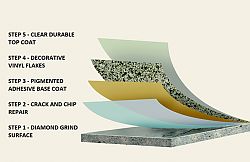 |
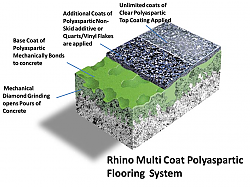 |
Our Five Step Application Process |
Polyaspartic Floor Coating Cut-Away |
Product Downloads
Rhino FastFloor™ (PDF)
Rhino FastFloor Color Chart (PDF)
Rhino Polyaspartic Color Chart (PDF)
Chem-thane DCP (PDF)
Cured Coating Properties- Epoxy vs. Polyurethane vs. Polyaspartic (PDF)
Polyaspartic Coating Chemical Test Results (PDF)
Polyaspartic Coatings FAQs
(click on the title for the answers)
What Exactly are Polyaspartics?
Polyaspartics were invented in the 1990's by a German chemical company named “Bayer” (the same company that makes the aspirin). Technically, polyaspartics are a type of polymer called “polyurea aliphatics”. Polyureas are two-part systems, meaning that they require a resin to be mixed with a catalyst to create the curing reaction that hardens and cures the material. Polyurea is what makes Polyaspartic so highly durable. Although polyaspartics have been available for many years, their use as commercial metal and floor coatings have been relatively recent.
How is the Polyaspartic you install different than the epoxy we all see at the big box stores?
Much like buying a fake Rolex on the streets of New York, the difference is that it doesn’t last long and doesn’t look as good as the real thing. The polyaspartic we use is pure unadulterated If it’s a commercial application, we also use a 4th Polyaspartic top coat. With all things, it’s not just the product we use that makes it so good, it’s the process and tooling we use to do good work. If your just trying to make something look a little better before you sell it, or you don’t use it very often, an epoxy at a box store should hold out long enough. We have seen hot tires stick and rip of the flooring folks went to work the next day.
A major home improvement store offers a 2-coat "Premium Floor Coating" at $2.25per square foot, however, they include the thickness of the flakes as part of their overall finished thickness. They also have a square foot minimum of 500 sq ft. This means that their "Premium Package" is actually 8-12 mils and for a 2 car garage that’s $1125.00 and less than half the thickness of our floors and it is not turn key. This same Home Improvement Company charges extra for crack repair and non-skid additive and by the time you add those into the price your paying the same thing as you are with us except your getting twice the thickness, durability and product. The flakes included at the home improvement store are added to the top coat and are therefore left exposed, rather than encapsulated, so that the overall durability of your coating is then only as strong as the flakes themselves. Trust us, you don't want that.
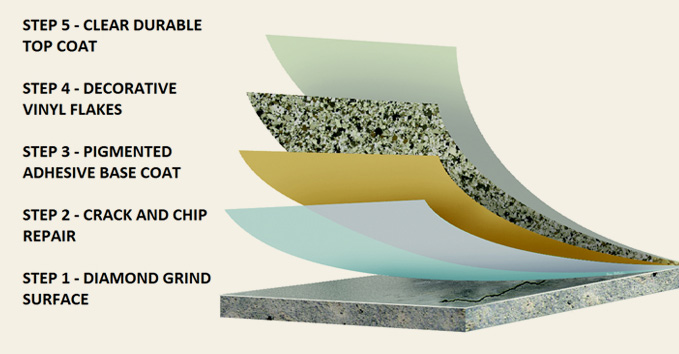
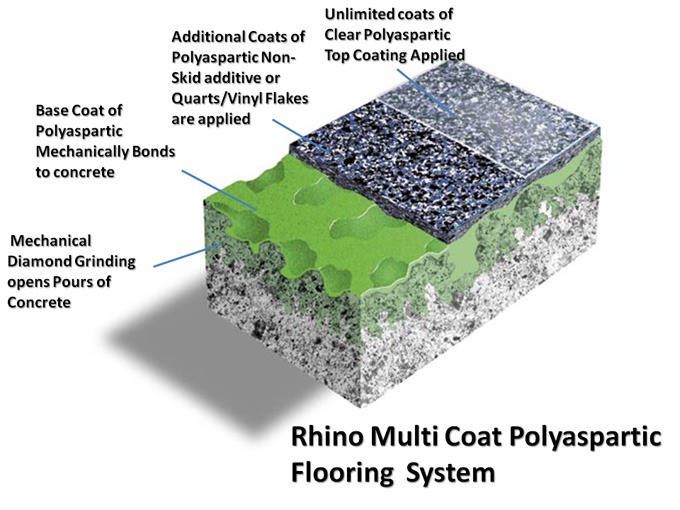